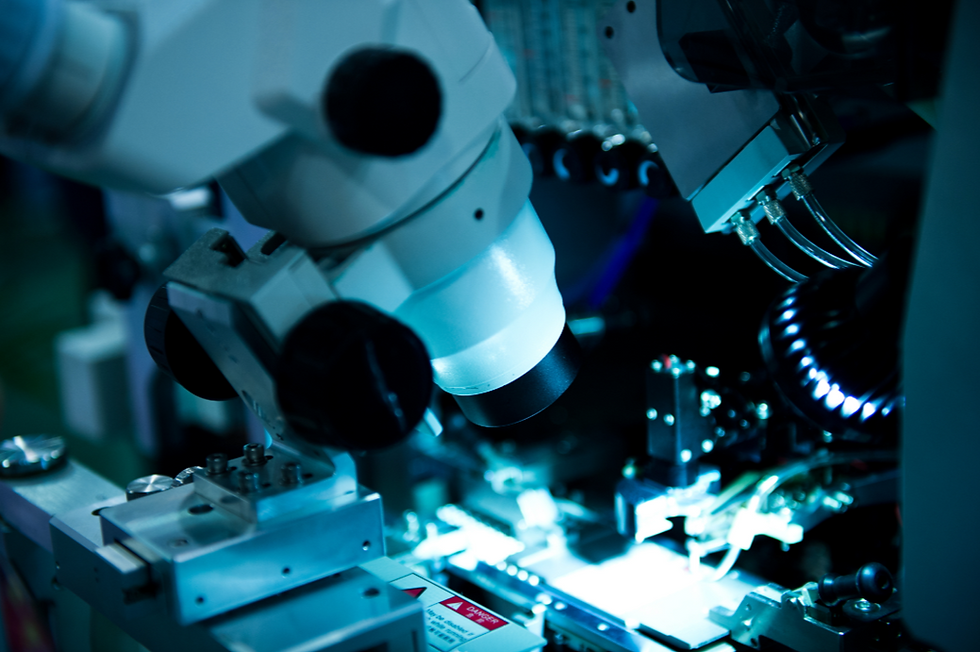
The semiconductor industry is viewed as among the most critical and technologically intensive enterprises because it manufactures integrated circuits- the base of all modern electronics. From smartphones and computers to medical devices and electric cars, semiconductors are already integrated into cutting-edge technologies. Chip manufacturing is complex and exacting, consisting of several stages in the process that can easily result in very expensive defects or decreased performance with contamination of any kind.
High-purity gases play an indispensable role in nearly every step of semiconductor fabrication; even very minor impurities can result in the complete degradation of the finished product. This paper illustrates the need for high-purity gases in three key areas of semiconductor manufacture: deposition, photolithography, and chamber cleaning.
Deposition Processes
These are methods where very thin films of materials are deposited on silicon wafers through CVD or PVD, which actually constitute the backbone of transistors and other electronic components. Gases of very high purity, such as silane (SiH₄), ammonia (NH₃), hydrogen (H₂), and oxygen (O₂) are used in CVD processes for depositing material such as silicon, silicon nitride, and silicon dioxide on the wafer.
Importance of Purity of Gases for Deposition:
Contamination Avoidance: Even trace levels of impurities in gases result in the deposition of unwanted particles or compounds in the film. Impurities of this kind give rise to defects, such as pinholes, rough surfaces, or non-uniform films that seriously deteriorate the semiconductor's performance and reliability.
Chemical Uniformity: Uniformity in gas purity ensures that the chemical reactions associated with CVD or PVD are uniform across a whole wafer. This leads to predictable, repeatable, and high-quality results in thin film formation-crucial to semiconductor device performance.
Minimum Defects: Because semiconductor nodes are on the nanoscale level-with transistors measured in nanometers-even one particle or defect caused by an impure gas can in fact create malfunctioning of the IC. Thus, extremely high-purity gases (99.999% or higher) are required.
Photolithography
The other essential process involved in semiconductor manufacturing is photolithography, which consists of the pattern transfer onto a silicon wafer using light and photoresist chemicals. Certain gases can be used during the process, like nitrogen and argon, to maintain a controlled atmosphere while the exposure and development process is going on. Ultra-pure hydrogen is utilized in extreme ultraviolet lithography, the latest photolithography technology.
Importance of Gas Purity in Photolithography:
Patterning Accuracy: Photolithography involves a high degree of accuracy in the nanometre length scale to etch patterns. Any trace of contamination of the gas interferes with the optical systems and, hence, causes distortion in the light path leading to incorrect patterning.
Photoresist Protection: High-purity nitrogen is used to furnish an inert atmosphere that protects the photoresist from contamination and oxidation during exposure. Contaminated gases can react with photoresists, leading to a change in its pattern or weakening its effectiveness.
Purification Light Source: EUV uses ultra-pure hydrogen as a cleaning agent to maintain the purity of the source optics. Hydrogen impurities may cause unwanted chemical reactions that could reduce the quality of the EUV light, which in turn may have adverse effects on the patterning process.
Chamber Cleaning
Before these semiconductor manufacturing devices can be used in wafer processing, residual materials from the last process may interfere with the manufacturing process. Residues of films on chamber walls and components are cleaned by plasma cleaning using high-purity fluorinated gases such as nitrogen trifluoride (NF₃) and sulfur hexafluoride (SF₆).
Importance of Gas Purity in Chamber Cleaning:
Effective Cleaning: Plasma cleaning cannot be effective unless the cleaning gases are of high purity to ensure residues without contaminating them with new contaminants. If impurities are in the cleaning gases, then foreign materials might be deposited on chamber surfaces that might later be transferred to wafers.
Process Efficiency: Cleaning the chamber with high-purity gases allows for an efficient cleaning process; therefore, the time to clean the chamber is reduced, while increasing all-around manufacturing throughput. A clean and contaminant-free environment is absolutely necessary in semiconductor production to guarantee high yields.
Etching
Etching is another critical stage of semiconductor fabrication where the unwanted material has to be removed from the intricate pattern on the wafer surface. Wet and dry etching methods, using high-purity gases such as chlorine (Cl₂), boron trichloride (BCl₃), and fluorinated gases, enjoy a common application in the industry.
Importance of Gas Purity in Etching:
This may also be in a form termed as selective etching. For example, the purity of the gases is very crucial in ensuring that the etching selects only certain materials to be etched without affecting other layers of the wafer. Impure gases may cause non-selective etching, resulting in defective features on the wafer.
Impurities may result in increased surface roughness, which affects the electrical properties of the semiconductor adversely and reduces the efficiency of the final chip. High-purity gases make sure that the results of the etching come out smoother and with more accuracy.
Conclusion
In the semiconductor fabrication process, high-purity gases are indispensable for every step: deposition, etching, lithography, and cleaning. Even trace contamination can lead to defects that substantially impair performance, yield, and reliability in the final product. With device complexities continuing to increase along with the ongoing miniaturization of transistor sizes, ultra-high-purity gases-99.9999% and above-have become more vital than ever. Maintaining stringency in gas purity ensures semiconductor manufacturers that their chips will have the desired reliability and performance to power the future of technology.
コメント